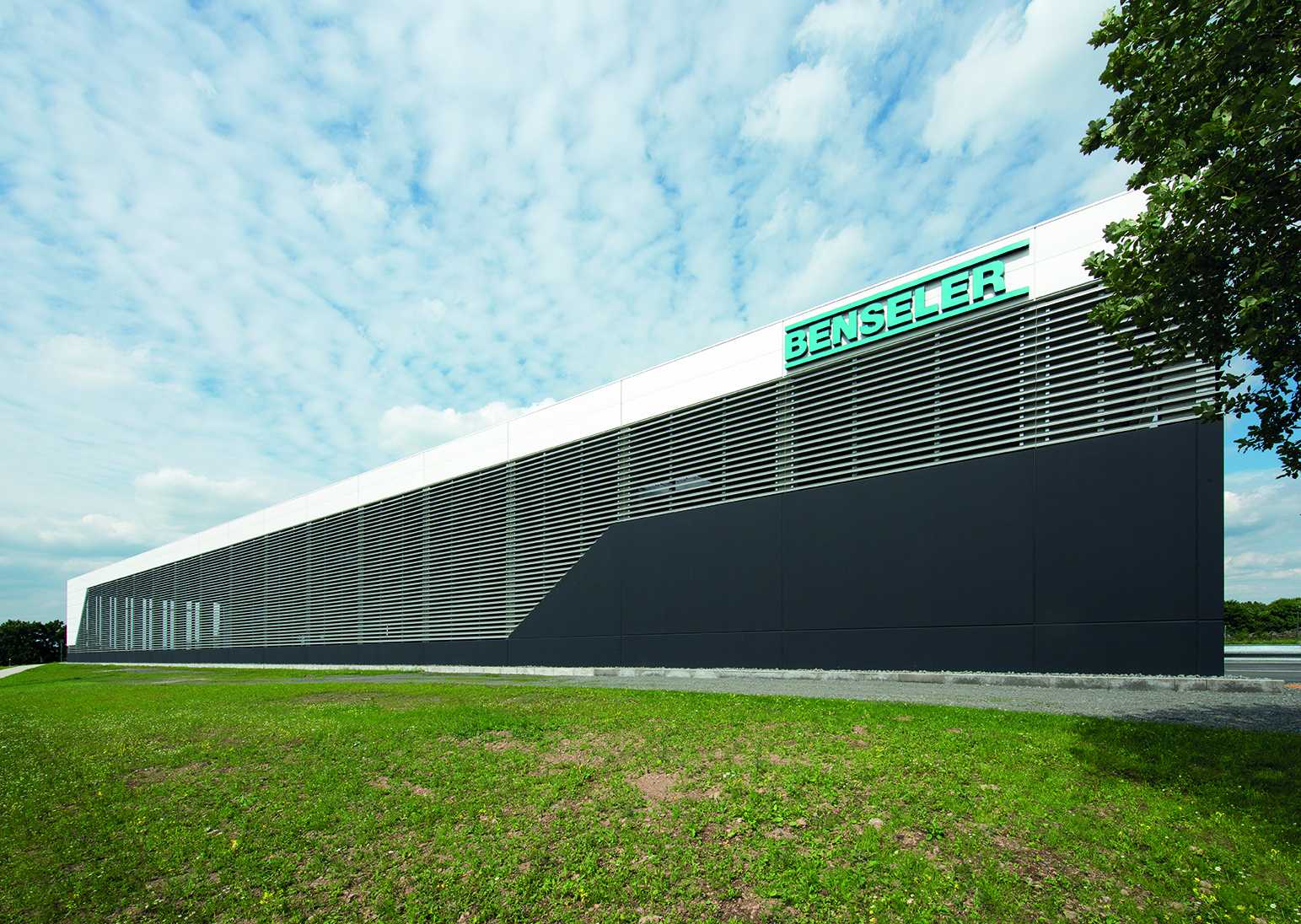
Projektdaten
Kategorie | Realisierte Bauwerke |
---|---|
BauherrIn | M.Werner GmbH & Co.KG Grundstücksgesellschaft mbH |
PlanerIn | UNIT4 GmbH & Co.KG |
Fertigstellung | 2015 - 2017 |
Ort | Lüdenscheid |
Bildnachweis | David Franck |
DER ENTWURFSGEDANKE
Der Neubau der Fertigungsstätte für Dünnschicht Korrosionsschutz-Systeme der Firma Benseler in Lüdenscheid in direkter Nachbarschaft der Autobahn A45, vereint in einem ein- bis zweigeschossigen Baukörper von 104 x 96 m die Produktions-, Support, Chemie, Labor, Lager, Logistik, IT-Zentrale, Testräume und Labors, Disposition und Vertrieb, Anliefer- und Büros, sowie Anlagen- und Prozesstechnikbereiche auf einer Gesamtfläche von ca. 11.200 m² in einem Bauvolumen von ca. 91.000 m³.
DIE KONSTRUKTION / ÖKONOMIE
Zur Evaluierung einer möglichst nachhaltigen, wirtschaftlichen und effektiven Bauweise, wurde in einem ersten Schritt unterschiedliche Konstruktionsarten vergleichend untersucht. Nach Auswertung der Varianten fiel die Entscheidung unter Berücksichtigung der vorhandenen umwelt- und brandschutztechnischen Auflagen, auf die Ausbildung des Tragwerks in klassischer Stahlbeton-Fertigteilbauweise.
Die Produktionshalle mit einer Grundfläche von ca. 102 x 48 m ist durch eine Stützenreihe in zwei stützenfreie Bereiche mit Spannweiten von je 24 m geteilt. Das mit geringen Neigungen ausgeführte Dach wurde mit Trapezblechen eingedeckt und umfasst die gesamte Produktionshalle. Ausgenommen davon ist der Dachbereich für die technische Nutzung, welcher auf der tieferen Höhe des Zwischengeschosses liegt und in Betonbauweise ausgebildet wurde. Alle Dachbereiche wurden mit umlaufender Attika in Form von Attikaträgern ausgeführt.
DIE FASSADE / GESTALTUNG
Bewusst wurden die unterschiedlichen Funktionen der Produktionsbereiche in der Fassadenwertigkeit und -farbigkeit ablesbar gestaltet. Durch das in seiner Höhenlage und Breite vertikal variierend umlaufende mäandrierende weiße Metallfassadenband, werden die dahinterliegenden Funktionseinheiten gefasst und bilden eine bauliche Einheit. Die somit endlos gestaltete Fassadenhaut tritt als bauliches Pendant in direkte Korrespondenz mit der Dynamik und Bewegung der direkt angrenzenden hoch frequentierten Autobahn A45.
Die Oberflächen der Produktionsstätte, wie auch die der Büro-, Labor- und Nebenbereiche spiegeln die Grundfarben des Oberflächenbeschichtungsspezialisten Fa. Benseler wieder.
Hierbei wurden die Farbwelten mit architektonisch ansprechenden Materialien belegt und in sinnvoller Weise Bauteile oder Konstruktionselemente des Industriebaus pointiert in das architektonische innenräumliche Erscheinungsbild integriert.
DAS RÄUMLICHE KONZEPT
Durch die architektonische Optimierung der Funktionseinheiten auf Grund des großen funktionsbedingten ebenerdigen Flächenbedarfs der Produktionshalle mit den direkt angeschlossenen Technik- und Versorgungsanlagen, dem Warenlager, der Qualitätssicherung mit den benötigten Labors und des Logistikbereiches, in dem durch eine vollständig überdachte Be- und Entladezone bis zu 70 Gigaliner pro Tag witterungsunabhängig abgefertigt werden können, konnte der Turnover des Produktions- und Warenflusses vom Wareneingang bis zum fertigen Produkt von durchschnittlich 48 Stunden und somit um 50% reduziert werden.
ENERGIE EFFIZIENZ / NACHHALTIGKEIT / KFW 70 HAUS
Beim Aufbau der neuen Produktion in Wibschla wurde im Besonderen, neben der Erreichung des KfW 70 Standards, darauf geachtet, die bestmöglichen Lösungen hinsichtlich Umwelt- und Ressourcenschonung umzusetzen. Durch eine entsprechende Kombination von Abluft- und Energierückführtechnik im Bereich der Anlagen und Prozesstechnik, gekoppelt mit einer intelligenten Gebäudetechnik, kann somit ein großer Teil der im Arbeitsprozess entstehenden Abwärme aufgefangen und wiederverwendet werden. Mit dieser Wärmeenergie wird die gesamte Vorbehandlung der energieintensiven Produktion, sowie ein Teil der Einbrennenergie der Öfen eingespart. Darüber hinaus wird durch den Einsatz von Wärmetauscher die benötigte separate Aktivkühlung der Brennöfen und die Klimatisierung des Verwaltungsbereiches, ohne zusätzliche Energieaufwendung, betrieben.
Der Produktionsverbrauch von Erdgas konnte somit drastisch gesenkt und die Energiebilanz massiv verbessert werden. Durch dieses effiziente Energierückgewinnungsverfahren wird die Verbrennung von 750.000 m³ Erdgas pro Jahr verhindert und somit der Ausstoß von 1,5 Mio. kg CO2 reduziert.