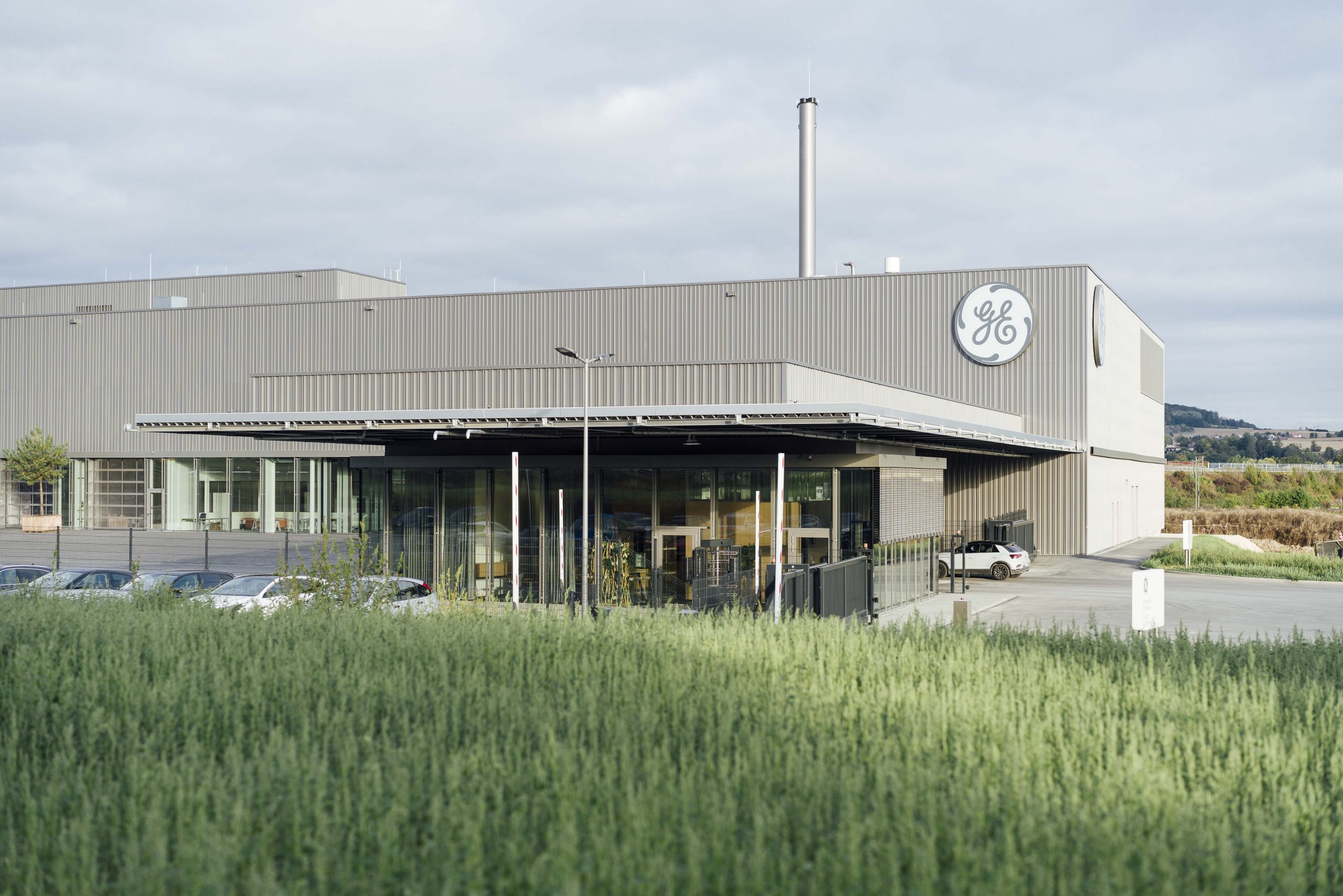
Projektdaten
Kategorie | Realisierte Bauwerke |
---|---|
BauherrIn | GE Additive |
PlanerIn | SCHMELZLE+PARTNER MBB ARCHITEKTEN BDA |
Fertigstellung | 07.2017 - 09.2019 |
Ort | Lichtenfels-Seubelsdorf |
Bildnachweis | Bernhard Kahrmann |
Vor 20 Jahren entwickelte Frank Herzog, der Erfinder des LaserCusing-Verfahrens, seinen ersten Prototypen und gründete das Unternehmen Concept Laser. Seit Dezember 2016 ist dieses Teil von GE Additive, einer Division des weltweit führenden digitalen Industrieunternehmens General Electric, und ist einer der weltweit führenden Anbieter von Maschinen und Anlagentechnik für den Metall-3D-Druck. Auf den von Herzog entwickelten Maschinen werden Triebwerk- und Turbinenteile für Flugzeuge, Motorenkomponenten für Kraftfahrzeuge oder zahnmedizinische Implantate gedruckt.
Auf 11,4 Hektar Gelände entsteht mit insgesamt ca. 42.200 m² der neue 3D-Campus. Dieser wird das weltweite Zentrum von General Electric für die Forschung, Entwicklung und Produktion von 3D-Metalldruckern. Der 3D-Campus ist insgesamt 420 m lang, 95 m breit und bis zu 22 m hoch. Direkt an der Autobahn gelegen bietet der neue Standort optimale logistische Voraussetzungen. Der Neubau besteht aus einem spitzwinkeligen Bürogebäude mit Schenkellängen von 180 und 130 Metern, sowie einer in diesen Winkel eingebetteten Produktionshalle mit 280 m Länge und 56 m Breite. An der Westseite schließt eine Parallelogramm-förmige Technik-Zentrale (Powerhouse) mit einer Überdachung der Pforte (Dach ca. 49 x 24 m) die Bebauung ab. Die Produktion ist an zwei Stellen über Verbindungsgänge an die Verwaltung angedockt.
Da sich das Gebäude im Schwemmgebiet des Obermains befindet, besitzt der Untergrund nur eine geringe Tragfähigkeit. Die Bodenplatte der Produktion wurde als Decke ausgebildet, die auf einem Trägerrost aufliegt. Dieser wird wiederum auf fast 500 Bohrpfählen abgelastet. Der Baugrund befindet sich außerdem auf historischem Gebiet, dort lebten einst die Kelten. Tatsächlich wurden Siedlungsreste aus verschiedenen Epochen – von der Bronzezeit bis zum Spätmittelalter – entdeckt. 400 m neben den Siedlungsresten legten die Archäologen zudem eine „kleine Grabgruppe“ frei. Einen besonderen Fund stellte ein 4.500 Jahre altes Körpergrab aus der „Glockenbecherzeit“ dar: Es belegt, dass rund 1.500 Jahre vor der Urnenfelderzeit bereits Menschen im Raum Seubelsdorf lebten.
Der neue Gebäudekomplex ist auf bis zu 700 Arbeitsplätze ausgelegt. Zuerst werden die rund 450 Mitarbeiter, die zurzeit noch in 21 verschiedenen Gebäuden arbeiten, an einem Standort vereint. Der Verwaltungsteil des 3D-Campus wird 2021 in Betrieb genommen.
Gemäß amerikanischem Standard läuft der komplette Zugang über die Pforte, die rund um die Uhr besetzt ist. Sowohl Besucher als auch Zulieferer melden sich hier an und werden in einem separaten Schulungsraum eingewiesen.
Die Produktion, gegliedert in zwei Hallenschiffe und einen mittigen Spine, besteht aus Stahlfachwerkträgern mit darüberliegendem akustisch gelochten Trapezblech. Metallkassetten mit vorgehängter Metallfassade aus individuell gekanteten Blechen sowie eine Pfosten-Riegel-Fassade und das Foliendach bilden den räumlichen Abschluss der Produktion. In südöstlicher Richtung ist ein uneingeschränkter Blick auf den oberfränkischen Gottesgarten mit der Basilika Vierzehnheiligen möglich.
In der untersten Ebene des Spine befinden sich dort, in unmittelbarer Nähe zu den Montagebereichen, produktionsnahe Büros, Besprechungsräume und Teeküchen für die Mitarbeiter der Produktion. Im 1. Obergeschoss sind die Sozialbereiche angeordnet. Umkleiden, Duschen, Toiletten sowie weitere Teeküchen, ein Game Room und Pausenräume sind ebenfalls dort zu finden. Die oberste Ebene des Spine ist reine Technikfläche. Hier erfolgt die Verteilung aller Medien zwischen Power House, Produktion und Verwaltung. Jede zweite Hallenstütze dient als Mediensäule und Anschlussmöglichkeit für Maschinenmontageplätze.
Auf einer Nutzfläche von fast 18.200 m² bietet die neue Produktionshalle ausreichend Platz für Montagearbeitsplätze unter modernsten Bedingungen. Alle Hallenbereiche sind mit großen Krananlagen mit 20 Tonnen Traglast ausgestattet. Weiterhin erleichtern Konsolkräne mit 1,6 Tonnen Traglast die tägliche Arbeit. In einem separaten Hallenteil kann die Abteilung „Research & Development“ die zukünftigen Produkte des Unternehmens weiterentwickeln und testen.
Eine integrierte Kalthalle ermöglicht witterungsunabhängig Be- und Entladevorgänge der LKWs. Die Krananlagen der Produktionsbereiche können durch Kranklappen auch diesen Bereich anfahren und beispielsweise fertig montierte Maschinen direkt auf das Fahrzeug zum Abtransport absetzen. Des Weiteren ermöglichen vier Verladerampen mit Unterfahrt mühelose Ladevorgänge von Fahrzeugen.
Das Powerhouse liefert die Technik für den gesamten 3D-Campus und ist über eine Medienbrücke mit dem restlichen 3D-Campus verbunden. Der Wärme-Kälte-Verbund besteht aus drei Stufen. Die erste Stufe beinhaltet eine reversierbare Wärmepumpe für Niedertemperaturwärme von 45/35°C. Die Primär-Wärmequelle ist die Maschinenabwärme aus der Produktion, die Abwärme aus dem Produktionsprozess wird voll ausgenutzt. Die Sekundär-Wärmequelle ist die Außenluft bis +6°C (Nutzung von Umweltenergie). Die Wärmepumpe besitzt im Heizfall eine Leistung von 1.200 kW. In der zweiten Stufe wird die Abwärme aus der Drucklufterzeugung mit Hochtemperaturwärme 70/50°C genutzt. Damit wird das Warmwasser für die Sozialräume und die Küche erzeugt. Es werden Lastspitzen im Heizfall abgedeckt. Diese Stufe wird bei Ausfall der Wärmepumpe überflüssig. Die Leistung aus der Abwärme beträgt 240 kW. Die dritte Stufe besteht aus einem Gasbrennwertkessel mit Hochtemperaturwärme 70/50°C und deckt im Heizfall die Spitzenlast ab, was zu einer Redundanz von Stufe 1 und 2 führt. Die Leistung beträgt 2.000 kW.
Auch die Kälteerzeugung erfolgt dreistufig. Stufe 1 beinhaltet Free Cooling für Maschinen und die Raumkühlung sowie eine Adiabate-Kühlung über Rückkühler. Die Leistung beträgt bis zu 3.000 kW. Stufe 2 kühlt durch den Entzug von Wärme über die reversierbare Wärmepumpe bzw. Kältemaschine. Bei gleichzeitiger Erzeugung von Wärme wird eine Kälteleistung von 1.200 kW erzeugt. Stufe 3 erzeugt Kaltwasser mit gleitender Kaltwassertemperatur mit einer Leistung von 2.400 kW.
Raumlufttechnische Anlagen für die Produktionshalle zur Deckung des hygienischen Außenluftwechsels und zur Wärme und Schadstoffabfuhr sind installiert. Die Wärmerückgewinnung der Abwärme aus der Produktion beträgt 75 – 80 % über Wärmeräder. Die Beheizung der Produktionshalle erfolgt mit Niedertemperatur 45/35°C über Betonkernaktivierung der Bodenplatte.