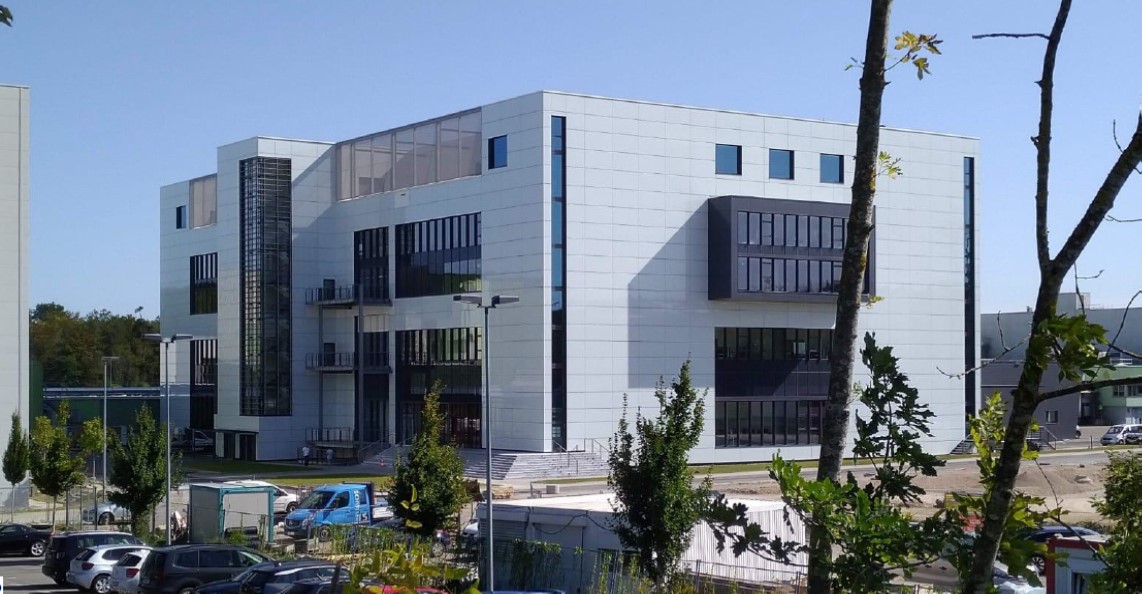
Projektdaten
Kategorie | Realisierte Bauwerke |
---|---|
BauherrIn | Takeda GmbH |
PlanerIn | HHP Architekten GmbH |
Fertigstellung | 11.2019 |
Ort | Singen |
Bildnachweis | Götz Poll |
HHP Hartwich Huber Poll Architekten GmbH mit Pharmaproduktionsgebäude der Firma Takeda GmbH in Singen. Die Aufgabenstellung für das Planungsteam, das auch aus einer großen Zahl von Fachplanern bestand, war die Entwicklung eines Gebäudes, in dem sehr komplexe Produktionsabläufe, die meist in Reinräumen erfolgen, auf mehreren Ebenen unterzubringen, um ein kompaktes Gebäude auf einer Restfläche, zwischen Bestandsgebäuden, unterzubringen.
Das Gebäude musste in die Logistikspange mit zentralem Materialförderband zum Hauptlager angebunden werden. Die Produktionsabläufe waren durch verglasten Flurwänden flurseitig einsichtbar zu machen.
Da das Gebäude mitten zwischen andere Produktionsgebäude einzufügen war, musste bei der Gründung auf eine erschütterungsarme Bohrpfahlgründung zurückgegriffen werden. Das umfangreiche Lastenheft wurde in einem Entwurf umgesetzt und es entstand das Produktionsgebäude W35/W36.
Der interne Kürzel W35/W36 steht für ein Gebäude, in dem ein Impfstoff für eine der großen Plagen der Zeit produziert werden soll, sobald die Zulassung dazu erfolgt. Etwa die Hälfte der Weltbevölkerung ist von der Infektionskrankheit betroffen, die nach WHO zu den 20 unterschätzten Krankheiten der Weltbevölkerung zählt.
Das Gebäude hat eine Kubatur von ca. 110.000 m³ und stellt somit einen großen Komplex in einem klein gegliederten Industriegebiet dar. Damit die tatsächliche Größe des Gebäudes nicht auf den ersten Blick erkannt wird, sind jeweils mehrere Geschosse zu einem Geschoss so zusammengefasst worden, damit aus einem Gebäude mit 8 Ebenen, incl. Untergeschoss optisch ein Gebäude mit 3 Geschossen wurde, die für den Betrachter weitaus kleiner erscheinen als es in Realität tatsächlich ist. Das Auge des Betrachters setzt bekannte Strukturen wie Geschossigkeit eines Gebäudes mit geistig hinterlegten Proportionen zusammen und realisiert somit ein bedeutend kompakteres Gebäude.
Aus dem vorgegebenen Produktionsablauf und der dafür notwendigen Platzierungen der Technik entstand ein Gebilde, dass eine zerklüftete Kubatur aufwies, die mit gestalterischen Maßnahmen so geordnet werden konnte, dass ein nahezu homogener Kubus entstand.
Die technischen Anlagen die zwingend im Freien stehen müssen, wurden mit Textilen Strukturen, die eine gewünschte Durchsicht aufweisen, überspannt. Diese Art von Sichtschutz lässt ein raumbildendes Element entstehen, das das gesamte Raumgefüge zusammen führt wodurch und die sehr einfache Gebäudeform entsteht.
Die Hülle des Gebäudes konnte somit sehr einfach gestaltet werden, was die Verwendung von großformatigen Ganzglasplatten zuließ. Die Oberfläche des Gebäudes ist damit eine leicht zu reinigende Struktur die später recycelt werden kann, da der Grundstoff Glas in einer sehr reinen Form vorliegt.
Die Umgebung, die für ein Industriegebiet sehr grün vorhanden ist, spiegelt sich in der Fassade im wahrsten Sinne des Wortes wider. Die Stimmung des Hegaus mit der häufigen Wolkenbildung wird direkt als Reflektion in der Fassade widergegeben.
Da die Produktion für 24/7 ausgelegt ist, wurde das Nachtdesign in die Ausarbeitung des Entwurfs einbezogen, damit auch im Dunkeln die einzelnen Gebäudeteile außen klar ablesbar und verständlich sind. Das Gebäude befindet sich parallel zu einer Einfallsstraße und markiert somit den bebauten Rand des Industriegebiets der dadurch besonders im Dunkeln zu erkennen ist, da die restlichen Industriebauten nachts nicht beleuchtet sind.
Die Fundamente des Gebäudes sind auf Grund der schlechten Bodenverhältnisse mit einer Pfahlgründung versehen. Die Struktur selbst ist eine Stahlbetonstützenkonstruktion mit Stahlbetonflachdecken, die in einigen Geschossen partiell gegen Stahlkonstruktionen ausgetauscht wurden. Im eigentlichen Dachgeschoss, das ein reines Technikgeschoss darstellt, wurde auf eine leichte Stahlkonstruktion als Dachtragwerk gewechselt.
Die Versorgung des Gebäudes mit den notwendigen Medien erfolgt über die Technikgeschosse mit den direkten Verbindungen zu den Produktionsgeschossen, die somit im Wechsel zueinander angeordnet sind und dadurch die kürzeste mögliche Verteilung ermöglichen.
Zur Energieeinsparung wird in kleinen Teilen das in Zisternen gepufferte Regenwasser verwendet, soweit die Produktionsprozesse dies zuließen. Ansonsten ist die Hülle mit sehr niedrigen U-Werten ausgeführt worden.
Die nachträgliche Bestückung der einzelnen Produktionsebenen von außen wird durch ein variables Plattformsystem gewährleistet, das so aufgebaut ist, dass jede der Plattformen unabhängig ausgebaut werden kann, um die Einbringung schwerster Gerätschaften bis 30 t in die oberen Geschossen ermöglichen zu können. Die dahinterliegenden Fassadenelements sind als öffenbare Tore in der bestehenden Fassadenrasterung konzipiert, dass diese nicht als solche erkannt werden.
Im Inneren des Gebäudes sind große Teile in den verschiedenen Reinraumklassen ausgeführt, die der Zulassung des Produktionsprozesses geschuldet sind, gleiches gilt für die Ausführung der Lüftungsanlagen und anderer technischer Anlagen, die hier nicht näher beschrieben werden.
Neben den Produktionsstätten mit deren Sanitärzonen sind auch die dafür notwendigen Bürostrukturen um diese Bereiche mit transparenten Glasflächen angeordnet, damit die Sichtbeziehungen direkt bestehen. Eine ganzheitliche Transparenz für Mitarbeiter und Besucher während der Produktion wurde von Anfang an angestrebt.
Das Gebäude wurde im Herbst 2019 feierlich übergeben und seit dem laufen die Zulassungsprozeduren für die Produktionsfreigabe des darin demnächst gefertigten Impfstoffes.
Die Planung erfolgte im 3D Modell und wurde per IFC Dateien an die beteiligten Fachingenieure und Bauherrn weitergeleitet, damit deren Planungen und Revisionsunterlagen darauf abgestimmt werden konnten.